![]() |
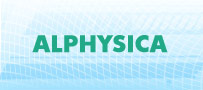 
|
 |
![]()
![]() |
![]()
AutoCAD meshing
The models take into account the interturn and interpancake heat transfer (in a limited number of coil cross-sections) and heat load distributions. This permits a qualitative analysis of the cryogenic system necessary to operate these different coils in normal operating conditions (plasma burn, plasma disruption) as well as during fast transients (safety discharge).
VENECIA modelling is supplemented with special 2D meshing techniques. One such technique implements AutoCAD tools in order to generate basic 2D finite-element meshes. These meshes are then treated by VENECIA so as to make them consistent with VENECIA models. The main steps are:
- A set of reference points is taken on an AutoCAD drawing.
- When AutoCAD is running, a dedicated package is started which is consistent with AutoCad and generates a number of additional command for building and modifying a 2D FE mesh.
- The resultant 2D mesh is in a standard AutoCAD format and can be treated with AutoCad tools.
- The 2D mesh is then post-processed by VENECIA in order to generate a 3D output mesh.
- The 3D mesh has a DXF format and is suitable for further AutoCAD treatment including generation of a realistic 3D image.

Figure 9. Cross-section No16 for the TF coil model based on AutoCAD meshing.
|
|
 |
![]()
 ![]() |
![]()
Germany (headquarters): Alphysica GmbH. Unterreut, 6, D-76135, Karlsruhe, Germany, Phone: +49 (0)163 904-85-61,
Fax: +49 (0)7219 444-26-55, E-mail: info@alphysica.com
![]()
USA: Alphysica Inc. 414, Jackson street,
San Francisco, CA 94111, USA, Phone/Fax: +1 415.230.23.63, E-mail:usa@alphysica.com
![]()
Russia: Alphysica Ltd. 55, ul. Mayakovskogo, 191025, St.Petersburg, Russia, Phone/Fax: +7 (812) 335-95-04, E-mail: russia@alphysica.com
Copyright © 1994-2010
| |
|
![]() |