![]() |
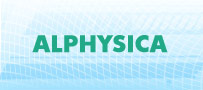 
|
 |
![]()
![]() |
![]()
ITER. Central Solenoid and Poloidal Field Coils
VENECIA models for the CS and Poloidal Field Coils (PFC) allow detailed simulations of the CS and PF winding packs thermohydraulic behaviour together with its cooling circuit under different operational conditions.
CS model provides:
- individual modelling in two-channel approach of 240 CICC's in a 1-D approximation for 6 CS winding sections;
- individual modelling of external pipes, cryolines, manifolds and heat exchangers in a 1-D approximation;
- the total number of different 1-D objects exceeds 1000;
- detailed individual description of different transient heat loads over 1-D objects;
- quasi-3D simulation of the CS winding sections via 2D modelling of 6 cross-sections of the CS conduits with insulation (the total number of mesh nodes exceeds 3,500,000);
- modelling of pressure-mass flow rate characteristics of pumps;
- modelling of a liquid helium bath.

Figure 3. Cooling scheme of the CS coil VENECIA model.

Figure 4. Cooling layouts and cross sections positions for the CS1L coil pancakes.

Figure 5. Temperature maps for the CS coil cross section #1 at different time points of simulation.
The PF magnet system model features:
- individual modelling in two-channel approach of all CICC's in a 1-D approximation for 6 PF coils;
- each PF's pancake is modelled as wounded by CICC using two-in-hand;
- individual modelling of external pipes, cryolines, manifolds and heat exchangers in a 1-D approximation;
- the total number of different 1-D objects exceeds 800;
- detailed individual description of different transient heat loads over 1-D objects;
- quasi-3D individual modelling each of six PF coils via 2D modelling of their corresponding cross-sections of the PF conduits with insulation (the total number of mesh nodes for 72 cross-sections exceeds 3,100,000);
- modelling of pressure-mass flow rate characteristics of control valves and pumps;
- modelling of a liquid helium bath.

Figure 6. Cooling scheme of the PF magnet system VENECIA model.

Figure 7. Cooling layout and 2D cross sections for the PF2 coil pancakes. About 23,500 mesh nodes for each of 12 sections (totally 282,000 nodes).

Figure 8. Temperature map for PF2 coil VENECIA model at 1.35s of 4th plasma pulse. Section #6.
|
|
 |
![]()
 ![]() |
![]()
Germany (headquarters): Alphysica GmbH. Unterreut, 6, D-76135, Karlsruhe, Germany, Phone: +49 (0)163 904-85-61,
Fax: +49 (0)7219 444-26-55, E-mail: info@alphysica.com
![]()
USA: Alphysica Inc. 414, Jackson street,
San Francisco, CA 94111, USA, Phone/Fax: +1 415.230.23.63, E-mail:usa@alphysica.com
![]()
Russia: Alphysica Ltd. 55, ul. Mayakovskogo, 191025, St.Petersburg, Russia, Phone/Fax: +7 (812) 335-95-04, E-mail: russia@alphysica.com
Copyright © 1994-2010
| |
|
![]() |